National Renewable Energy Laboratory
NREL Newsroom
NREL: 35 Years of Clean Energy Leadership
Thirty-five years ago, when President Jimmy Carter opened the Solar Energy Research Institute (SERI) in Golden, Colorado, gasoline cost 62 cents a gallon, and solar power about $100 a watt.
Now, in the summer of 2012, the price of gasoline at the pump is $3.89 per gallon, the installed cost of solar power about $4 a watt.
That's a six-fold increase in the cost of gasoline, and a 95% reduction in the cost of solar. And with solar and wind energy growing by about 35% a year, and biofuels burgeoning, the laboratory in Golden is more vital than ever.
After 14 years as a solar institute, SERI achieved national lab status in 1991 under President George H. W. Bush. SERI became NREL, the U.S. Department of Energy's (DOE) National Renewable Energy Laboratory.
35 Years of Innovations, Breakthroughs, Discoveries

NREL's 327-acre main campus got an infrastructure boost in 2006 and 2007 when projects in the pipeline were accelerated. On the right, beyond the solar panels, is the Research Support Facility, recently tagged as the top net-zero energy building in the world.
Credit: Dennis Schroeder
Credit: Dennis Schroeder
What a 35 years it's been.
From its start on July 5, 1977, to today, NREL has pushed the boundaries of what's possible, leading the way to a clean energy future.
Wind turbines have grown from farmhouse curiosities to multi-megawatt behemoths.
NREL scientists inaugurated the era of the super-efficient multi-junction solar cell and combined those cells with lenses that concentrate the sun's rays by 500 times to multiply the power of photovoltaics.
The laboratory worked with industrial partners to lower the price of enzymes used to refine alternative biofuels by 97%.
And NREL scientists found ways to get two electrons from a photon of light; discovered a cost-effective way to virtually eliminate wasteful reflection off a solar cell; helped engineer an economic way to place transparent solar cells in window glass; engineered ways to get biofuels and hydrogen from algae; mapped renewable energy resources in dozens of countries; came up with new standards for aerodynamic wind turbines and concentrating solar power; and set the bar higher for sustainable buildings.
NREL researchers have won 52 R&D 100 awards — the "Oscars of Invention." That places NREL among the top national labs in R&D 100 awards per employee. Just this year, NREL won two: one for the highest-efficiency solar cell, and another for a revolutionary new type of air conditioning that uses 75% less energy than typical systems and can work in any climate.
From Rented Space to the Laboratory of the Future

NREL's National Wind Technology Center hosts giant turbines, which manufacturers throughout the world bring to the site for testing and certification.
Credit: Dennis Schroeder
Credit: Dennis Schroeder
From its origins in rented office space, NREL has expanded to a 327-acre campus that is a model for what a sustainable, green office park can look like.
"When I bring visitors on the site, I often tell them that when I came to SERI, this site was 300 acres of nothing but sage brush and rattlesnakes," said Stan Bull, NREL's former associate director for Science and Technology. "But look at it now."
Today, the NREL campus is a living model of sustainability, hosting hundreds of architects, planners, and lawmakers each year, along with a multitude of scientists from around the world.
It wasn't always so.
"The people who joined SERI early, who suffered through the great swings of support and inattention in the 1980s, were like monks in a monastery keeping the candle of hope and dedication burning while nobody else cared," said Art Nozik, an NREL senior research fellow emeritus whose breakthroughs on singlet fission opened the door to greater solar cell efficiency. "Today, when the awareness and importance of our mission is understood and appreciated by a large fraction of the world's population, we can be confident that we can move forward at an accelerated rate to help our society and planet to survive and flourish."
Ron Judkoff arrived in 1978, as the organization's first building energy efficiency scientist. "Back then, we were all in rented space, and when NREL built its first major building on campus, the Field Test Laboratory Building, no one thought to invite our small group of building energy efficiency scientists and engineers into the process," recalled Judkoff, who is now NREL's principal program manager for building energy research. "In fact, most of the staff and management probably thought the term 'building science' was an oxymoron."
Last month, Construction Digital, a monthly online magazine, named NREL's Research Support Facility (RSF) — a 326,000-square-foot building housing 1,300 employees — the top net-zero energy building in the world. "Net zero" means the building uses no more fossil-fuel-based energy in a year than it makes up for in on-site renewable energy. In all, the RSF has received more than 30 awards for sustainable design and construction.
Now, with several buildings that have achieved lofty LEED (Leadership in Energy and Environmental Design) status, the technologies developed by NREL and its industrial partners are found on the campus and in the world market. The "SolarWall" transpired collector, light louvers, electrochromic and thermochromic windows, thermal storage walls, and NREL's Open Studio software tools that simplify optimal energy design, are getting friendly receptions in the marketplace.
"I expect the awards to keep coming, and our campus to serve as a shining example of energy efficiency throughout the world for many years to come," Judkoff said.
Origins Traced to 1970s Oil Embargo

The sun hits the commemorative medallion on the floor of NREL's Science and Technology Facility (S&TF) at solar noon on July 5, 2012. The medallion was placed in the S&TF in 2006 to commemorate the anniversary of the lab in 1977, and the day in 1991 when President George H.W. Bush elevated the institute to National Lab Status.
Photo by Dennis Schroeder / NREL
Photo by Dennis Schroeder / NREL
SERI was approved by Congress and championed by President Carter in large part because of the oil embargo that pushed the price of gasoline from about 36 cents a gallon in 1972 to 62 cents in 1977.
From a focus on solar energy, NREL has grown to also include cutting-edge breakthrough research in wind, biofuels, energy efficiency, transportation, and geothermal energy.
Walt Musial was hired in 1988 as a testing engineer at a time when many of the U.S. wind power companies were going bankrupt because of canceled tax credits.
"The industry was moving to Europe, and NREL's National Wind Technology Center [NWTC] was one of the last safe havens where good-quality research was being done to explore big problems still facing the technology," Musial recalled.
NREL's wind center became the go-to site for companies, both foreign and domestic, to test their turbines and blades in the wind blowing down from the foothills of the Rocky Mountains and in the NWTC's dynamometer.
Not Just a Research Lab, but a Factor in the Marketplace
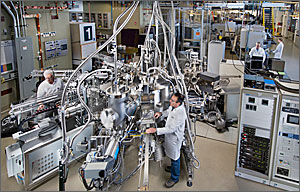
Two scientists work on a project to enhance the efficiency of thin-film solar cells at NREL's Process Development and Integration Laboratory, which helps private companies boost the performance of their cells and modules.
Credit: Dennis Schroeder
Credit: Dennis Schroeder
In its early years, SERI/NREL was a research lab that didn't involve itself in the realities of the marketplace. That changed in the early 1990s as NREL reached out to industry to help turn science into technology, working with the private sector to ramp up and bring renewable energy and energy efficiency to market.
Many of today's top solar companies percolated their ideas in the DOE Incubator program run at NREL.
NREL has been issued 262 patents and has agreements with 305 industry partners, 64 universities, and 33 not-for-profit organizations. It currently has 116 Cooperative Research and Development Agreements (CRADAs) with industry.
An International Reach; a Helping Hand in Disasters
NREL's reach spreads across five continents — from wind and solar studies in Indonesia to biofuel-powered vehicles in Antarctica.
NREL's Roger Taylor and Dick DeBlasio recall that in the wake of the Earth Summit in Rio de Janeiro in 1992, they implemented the first stage of what later became a Brazilian national program to deploy solar and small wind power systems in communities without electricity in rural Brazil. "Luz para Todus" (Light for All) became a multi-year rural electrification program after the installation of more than 100 lighting, water pumping, and health clinic systems. "Our work in Brazil was very rewarding and fun," said DeBlasio, a chief engineer. "I started here in May of 1978, but it seems like yesterday."
NREL scientists and engineers have helped rebuild communities devastated by hurricanes, floods and tornadoes — showing how to bring sustainable energy and architecture to cities and towns, from tornado-ravaged Greensburg, Kansas, to New Orleans, flooded in the wake of Hurricane Katrina.
Renewable Energy's Growth Has Exploded
In the 35 years that NREL has led the way to a clean energy future, renewable energy has exploded:
- Installed renewable energy tripled between 2000 and 2009 in the United States and globally.
- While renewable energy comprised 2% of all new electrical capacity installations in the United States in 2002, by 2009 renewable energy comprised 55% of all new installations.
- Installed wind energy capacity increased by a factor of 14 between 2000 and 2009 in the United States.
- The weighted average price of wind power in the United States fell to 4.4 cents per kilowatt hour, making it cost competitive with fossil fuels.
- The United States leads the world in wind energy capacity at more than 35 gigawatts.
Just in the past decade, solar energy generation quadrupled in the United States. The annual growth rate of installed solar photovoltaic electricity capacity was 39%, while wind energy capacity grew by 34% a year.
Bull recalls the early days as "a mixture of wild-eyed hopes and utter disappointment," as the lab at first grew rapidly, then "declined precipitously overnight" when half the staff was laid off. Now, more than 2,000 people are employed at NREL.
"SERI/NREL has been and I think always will be a special place because the staffers have such a deep-seated dedication and commitment to the vision and mission," Bull said. "Just the name NREL is an incredible 'door opener' both nationally and internationally. It's almost frightening at times the impact the name alone has on acceptance in the world of energy."
Learn more about NREL's 35 years of innovation
.

— Bill Scanlon
Posted originally by NREL. Please follow us on Twitter and "like" us on Facebook!